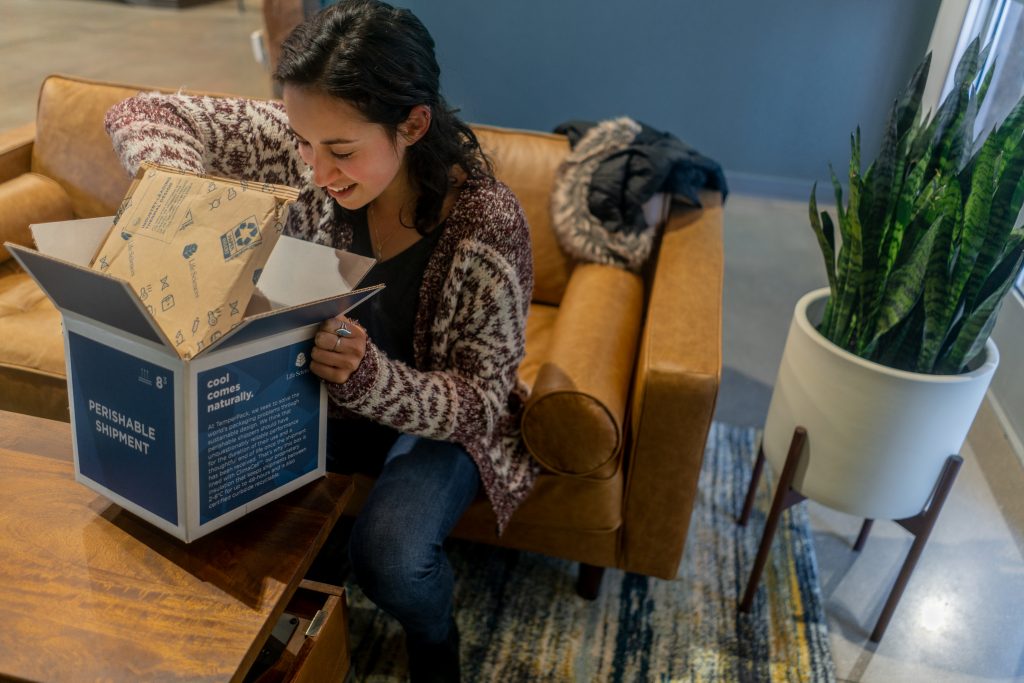
TemperPack Adds to SJF Portfolio Carbon Mitigation
The updated carbon impact model reflects the addition of TemperPack and increased carbon mitigation across SJF's portfolioTemperPack, headquartered in Richmond, VA, brings sustainable cold-chain packaging technology to companies that ship perishable goods such as food (meal-kits, grocery delivery, etc.) and pharmaceuticals. TemperPack is at the cutting edge of sustainable packaging and is empowering companies and their consumers to make a lasting environmental impact by displacing toxic polystyrene (Styrofoam®) alternatives.
The Challenge
In the United States, packaging waste represents one-third of all municipal trash, costing local governments billions each year in disposal costs[i]. A growing segment in the packaging industry, cold-chain packaging including temperature-controlled containers keep products like food and pharmaceuticals fresh and protected from the elements during the journey to the end consumer.
Over the past several decades, cold-chain packaging has been dominated by Expanded Polystyrene (EPS) foam products, like Styrofoam. The process by which Styrofoam is made is extremely detrimental to the environment: the EPA reports that the Styrofoam manufacturing process is the fifth largest source of hazardous waste in the United States[ii]. Furthermore, EPS is energy intensive to manufacture and is made from petroleum products, meaning it has an outsized carbon footprint. Beyond its environmental impacts, it is also a health concern: its constituent parts (Benzene and Styrene) are known carcinogens and have been shown to impact neurological function[iii].
As an illustration of the negative impacts of polystyrene, take, for example, its interaction with our oceans and coastlines. Polystyrene fragments easily and often and endures in the environment over time (estimates from 50 years in a marine environment to hundreds of years in terrain environments and landfills)[iv]. Microscopic pieces of polystyrene slip through the filtration systems of water treatment plants and make their way into the oceans where they often pick up pieces of biological material, like algae, thus smelling and feeling like food for small marine animals[v]. These plastics are ingested by small marine animals and then move up the marine food chain as these animals are eaten, and so on. The presence of polystyrene can threaten the health of these marine animals and their ecosystems, the health of humans who end up eating these marine animals, and the economic health of fishing communities[vi].
Polystyrene is considered to be so hazardous that more than 140 regulations restricting the usage of single-use plastics have been passed, with cities from San Francisco, New York City, and Los Angeles to Washington, D.C., Minneapolis, and Portland (OR) banning its use outright[vii].
The Solution
TemperPack has created and proven the viability of a sustainable design solution to the social and environmental problem EPS poses. Displacing Styrofoam is not just a byproduct of TemperPack’s operations and business success but is an integral piece of its business model. This pursuit led to the development of ClimaCell®, the first packaging material that not only offers sustainability advantages over Styrofoam but also matches its functionality and scalability. The company recognizes that too often, sustainability-minded products are not widely adopted because they fail to match the functionality of the incumbent products or are not cost competitive at scale. TemperPack developed the supply chain and manufacturing of ClimaCell to achieve high volumes and rapid scalability, while delivering on the core product performance and cradle-to-grave sustainability.
The Carbon Impact Report
Every year, SJF Ventures performs an analysis of the carbon emissions avoided by SJF portfolio companies. SJF originally added TemperPack to our 2018 model update, and in each year since, the analysis has found that TemperPack is indeed making a meaningful environmental impact.
To understand TemperPack’s emissions, the SJF team performed a two-stage life cycle analysis encompassing raw material emissions and manufacturing emissions. As the raw materials used in TemperPack’s products have changed, SJF has updated the model accordingly. This analysis looks at greenhouse gas emissions avoided from using more environmentally-friendly materials, as well as manufacturing techniques. As mentioned above, the processing/production of Styrofoam is also one of the largest sources of hazardous waste in the U.S., but this impact is not captured in the CO2 model. Additionally, TemperPack ClimaCell kits ship flat, decreasing the number of trucks required to ship the same quantity of units of EPS foam packaging solutions (6,000 fewer full trucks, in fact, in 2018). With that said, these emissions mitigated due to logistics and transportation are also not captured in the model.
In 2018, TemperPack’s raw material emissions displacement was driven by its use of textile waste in its fiber product. Textile waste accounted for 73% of total product weight and since it was a direct repurposing of material destined to be discarded, TemperPack was able to claim zero emissions for those salvaged materials. By 2019, TemperPack’s product mix changed, with greater emphasis on its fully-recyclable ClimaCell product. SJF’s model of TemperPack’s raw material emissions has been adjusted accordingly and is now calculated per ClimaCell kit sold.
On the manufacturing side, EPS container manufacturing is an energy-intensive molding process compared to the relatively simple assembly of TemperPack’s ClimaCell containers.
The Results
In total, TemperPack’s sustainable cold-chain packaging solutions displaced 4.6 million pounds of Expanded Polystyrene (EPS) foam, or Styrofoam in 2019. This amounted to the displacement of over 7,000 metric tons (~16 million pounds) of CO2 equivalent. TemperPack’s mitigation total is composed of displacing over 5,000 metric tons of CO2 equivalent from raw material emissions as compared to EPS foam and over 2,000 metric tons in manufacturing emissions.
TemperPack’s 7,000 metric tons of CO2 equivalent avoided contributed to SJF’s 2.78 million metric tons of CO2 equivalents avoided from all portfolio companies in 2019. Using updated equivalencies from the EPA, this carbon reduction is equivalent to 44 million urban tree seedlings grown for 10 years, 3.6 million acres of U.S. forests storing carbon for one year, or 602 thousand cars taken off the road for one year.
The Future
SJF is excited about the positive impacts TemperPack has had these last two years and is even more motivated by the company’s potential opportunity to further take down polystyrene in 2020 and beyond. Specifically, this report analyzes the carbon impact of TemperPack’s ClimaCell products that were sold during the 2019 year. TemperPack launched the ClimaCell product in 2018 – a fully curbside recyclable cold-chain solution – and plans to continue to grow this and other innovative product lines. In July 2019, TemperPack was awarded its first ClimaCell-related patent by the U.S. Patent Office. SJF looks forward to our investment partnership with TemperPack in its continued commercial and impact-oriented growth.
Sources
[ii] Rutgers University / Household Hazardous Waste Management
[iii] U.S. Environmental Protection Agency, National Technical Reports Library, U.S. Department of Commerce
[iv] Institute for European Environmental Policy